
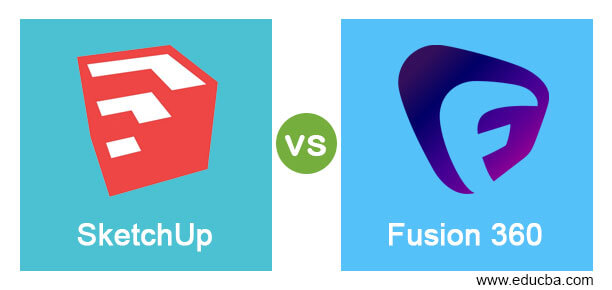
I tend to go for screws over friction fit if possible, just because it's much easier to account for tolerances and you can fix hole sizes with drills, taps, and inserts if necessary. The measurements on screen and in reality will always be slightly off (no matter what manufacturing method is used).
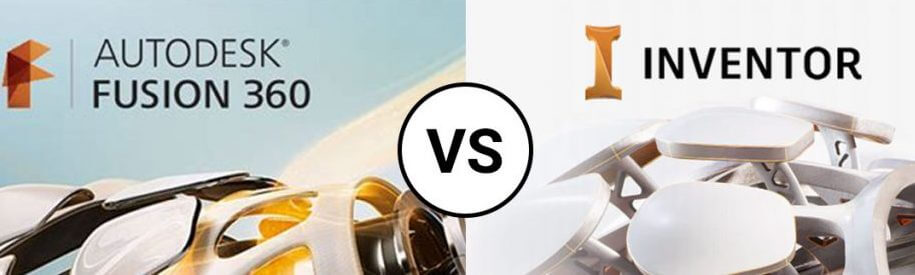
Just like how colors on screen and on a printed piece of paper don't quite match. You could also use a calibration cube and math to adjust for expansion and contraction.*

You can design for press fit parts, but you will likely need to either experiment with sizes until you dial in the tolerances, or create a calibration print to test them. You would need to model in the holes before you print. You aren't limited by anything as long as you are willing to experiment.ģD printing has a few caveats for production that you need to be considerate of when you design for it:ģD prints usually aren't solid, so drilling into them won't work the same way as drilling into wood or metal. It really depends on how you want to assemble it and print it.
